Jak smarować narzędzia pneumatyczne?
Smarowanie narzędzi pneumatycznych jest kluczowym elementem ich konserwacji, który wpływa na ich wydajność oraz żywotność. Właściwe smarowanie nie tylko zmniejsza tarcie pomiędzy ruchomymi częściami, ale także chroni przed korozją i zanieczyszczeniami. Pierwszym krokiem w procesie smarowania jest wybór odpowiedniego smaru, który powinien być dostosowany do specyfiki danego narzędzia. W przypadku narzędzi pneumatycznych najczęściej stosuje się smary na bazie oleju mineralnego lub syntetycznego, które charakteryzują się dobrą lepkością oraz odpornością na wysokie temperatury. Ważne jest również, aby nie stosować zbyt dużej ilości smaru, ponieważ może to prowadzić do zatykania układów pneumatycznych oraz obniżenia efektywności działania narzędzia. Regularne przeglądy i czyszczenie narzędzi przed smarowaniem są równie istotne, ponieważ pozwalają usunąć wszelkie zanieczyszczenia, które mogą wpłynąć na jakość smarowania.
Jakie są najlepsze metody smarowania narzędzi pneumatycznych
Wybór odpowiedniej metody smarowania narzędzi pneumatycznych ma kluczowe znaczenie dla ich prawidłowego funkcjonowania. Istnieje kilka popularnych metod, które można zastosować w zależności od rodzaju narzędzia oraz jego przeznaczenia. Jedną z najczęściej stosowanych metod jest manualne smarowanie, które polega na aplikacji smaru bezpośrednio na ruchome części narzędzia za pomocą pędzelka lub strzykawki. Ta metoda jest szczególnie skuteczna w przypadku mniejszych narzędzi, gdzie precyzyjne dozowanie smaru jest kluczowe. Inną popularną metodą jest wykorzystanie systemów automatycznego smarowania, które są montowane w większych narzędziach przemysłowych. Takie systemy dozują odpowiednią ilość smaru w regularnych odstępach czasu, co znacznie ułatwia konserwację i zapewnia optymalne warunki pracy. Niezależnie od wybranej metody ważne jest, aby regularnie kontrolować stan smarowania oraz wymieniać zużyty smar na świeży.
Jak często należy smarować narzędzia pneumatyczne
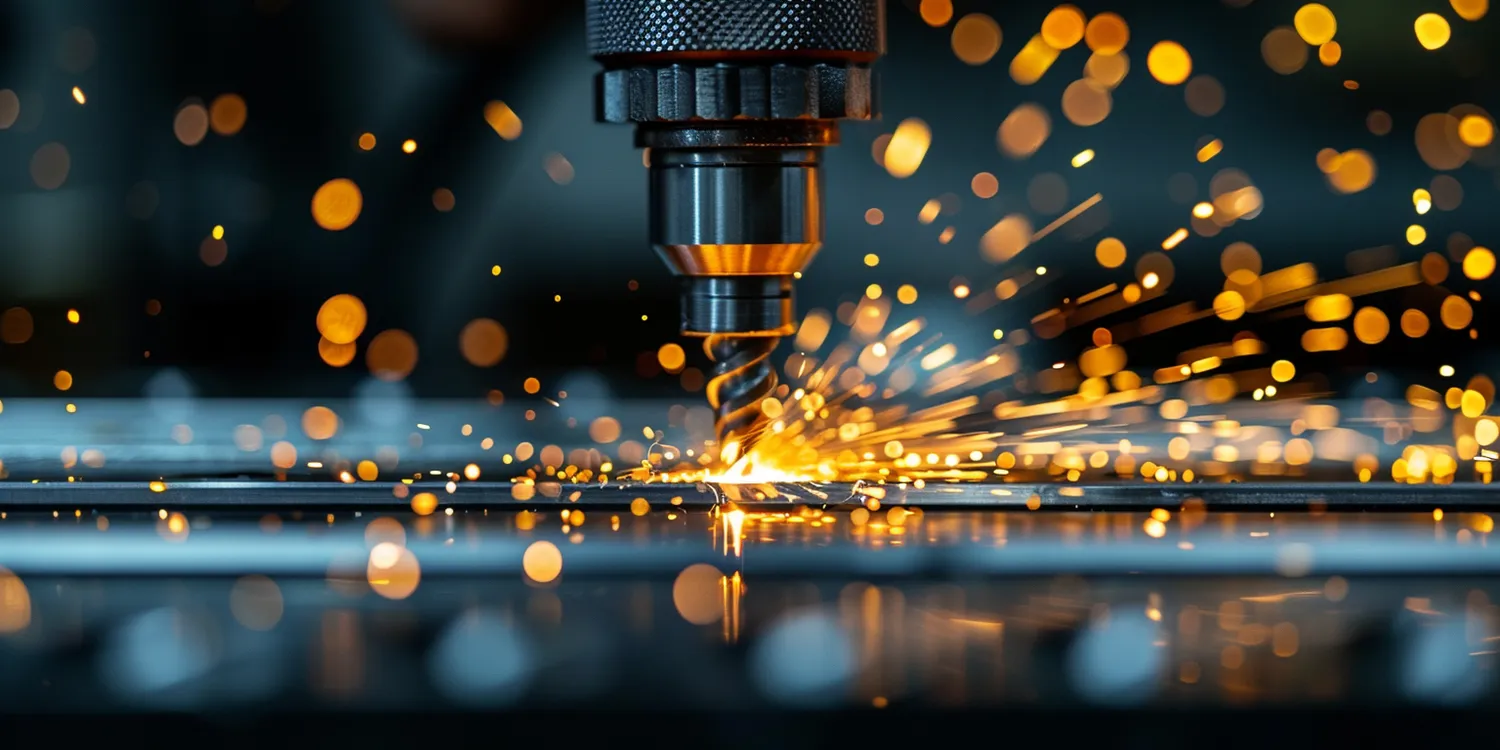
Częstotliwość smarowania narzędzi pneumatycznych zależy od wielu czynników, takich jak intensywność użytkowania, rodzaj wykonywanych prac oraz warunki pracy. W przypadku narzędzi używanych w warunkach przemysłowych lub przy dużych obciążeniach zaleca się regularne sprawdzanie stanu smarowania co kilka dni lub nawet codziennie. Z kolei w przypadku domowych zastosowań lub sporadycznego użytkowania wystarczy przeprowadzać konserwację co kilka tygodni lub miesięcy. Ważne jest również dostosowanie częstotliwości smarowania do specyfiki danego narzędzia – niektóre modele mogą wymagać częstszego uzupełniania smaru ze względu na swoją konstrukcję lub zastosowane materiały. Oprócz regularnego smarowania warto również zwracać uwagę na inne aspekty konserwacji, takie jak czyszczenie filtrów powietrza czy kontrola stanu uszczelek.
Jakie są skutki niewłaściwego smarowania narzędzi pneumatycznych
Niewłaściwe lub nieregularne smarowanie narzędzi pneumatycznych może prowadzić do wielu negatywnych konsekwencji, które wpływają zarówno na wydajność pracy, jak i trwałość samego sprzętu. Przede wszystkim brak odpowiedniego smaru zwiększa tarcie pomiędzy ruchomymi częściami, co może prowadzić do ich szybszego zużycia oraz awarii. W skrajnych przypadkach może to skutkować całkowitym zatarciem silnika lub innych kluczowych elementów narzędzia, co wiąże się z kosztownymi naprawami lub koniecznością zakupu nowego sprzętu. Ponadto niewłaściwe smarowanie może prowadzić do gromadzenia się zanieczyszczeń wewnątrz układu pneumatycznego, co dodatkowo obniża efektywność działania urządzenia. Warto również zauważyć, że nadmiar smaru może powodować problemy z działaniem mechanizmów pneumatycznych oraz prowadzić do wycieków oleju, co jest szkodliwe zarówno dla samego sprzętu, jak i dla środowiska naturalnego.
Jakie są najczęstsze błędy przy smarowaniu narzędzi pneumatycznych
Podczas smarowania narzędzi pneumatycznych wiele osób popełnia typowe błędy, które mogą negatywnie wpłynąć na ich funkcjonowanie. Jednym z najczęstszych błędów jest stosowanie niewłaściwego rodzaju smaru. Wiele osób nie zdaje sobie sprawy, że nie każdy smar jest odpowiedni do narzędzi pneumatycznych, co może prowadzić do ich uszkodzenia. Ważne jest, aby wybierać smary specjalnie przeznaczone do zastosowań pneumatycznych, które charakteryzują się odpowiednią lepkością oraz odpornością na wysokie temperatury. Kolejnym powszechnym błędem jest nadmierne smarowanie narzędzi. Choć wydaje się, że więcej smaru zapewni lepszą ochronę, w rzeczywistości może to prowadzić do zatykania układów pneumatycznych oraz obniżenia efektywności działania narzędzia. Zbyt duża ilość smaru może również powodować gromadzenie się zanieczyszczeń, co negatywnie wpływa na wydajność pracy. Inny błąd to brak regularnych przeglądów i konserwacji narzędzi. Wiele osób zapomina o tym, że regularne czyszczenie i kontrola stanu technicznego są kluczowe dla długowieczności sprzętu.
Jakie narzędzia i akcesoria są potrzebne do smarowania narzędzi pneumatycznych
Aby prawidłowo smarować narzędzia pneumatyczne, warto zaopatrzyć się w odpowiednie narzędzia i akcesoria, które ułatwią ten proces. Przede wszystkim niezbędny będzie odpowiedni smar, który powinien być dostosowany do specyfiki danego narzędzia. Warto również zainwestować w aplikatory smaru, takie jak strzykawki czy pędzelki, które umożliwiają precyzyjne dozowanie smaru na ruchome części. Dobrze jest mieć także dostęp do zestawu kluczy oraz innych narzędzi ręcznych, które mogą być potrzebne do demontażu elementów narzędzia w celu ich dokładnego wyczyszczenia i nasmarowania. W przypadku większych narzędzi przemysłowych warto rozważyć zakup systemu automatycznego smarowania, który znacznie ułatwia konserwację poprzez regularne dozowanie odpowiedniej ilości smaru. Oprócz tego przydatne będą również materiały eksploatacyjne, takie jak filtry powietrza czy uszczelki, które należy regularnie wymieniać w celu zapewnienia optymalnej pracy narzędzi.
Jakie są zalety stosowania systemów automatycznego smarowania w narzędziach pneumatycznych
Stosowanie systemów automatycznego smarowania w narzędziach pneumatycznych przynosi wiele korzyści zarówno dla użytkowników indywidualnych, jak i dla firm przemysłowych. Przede wszystkim automatyczne systemy smarowania zapewniają stałe dozowanie odpowiedniej ilości smaru, co eliminuje ryzyko niewłaściwego smarowania spowodowanego ludzkim błędem. Dzięki temu można znacznie zwiększyć efektywność działania narzędzi oraz przedłużyć ich żywotność. Kolejną zaletą jest oszczędność czasu – użytkownicy nie muszą regularnie kontrolować stanu smarowania ani ręcznie aplikować smaru, co pozwala skupić się na innych zadaniach. Automatyczne systemy często są również bardziej precyzyjne w dozowaniu smaru niż tradycyjne metody manualne, co przekłada się na lepsze wyniki pracy. Dodatkowo wiele nowoczesnych systemów automatycznego smarowania jest wyposażonych w czujniki monitorujące poziom smaru oraz stan techniczny narzędzi, co pozwala na bieżąco kontrolować ich kondycję i reagować na ewentualne problemy.
Jakie są różnice między różnymi rodzajami smarów do narzędzi pneumatycznych
Wybór odpowiedniego rodzaju smaru do narzędzi pneumatycznych ma kluczowe znaczenie dla ich prawidłowego funkcjonowania i długowieczności. Na rynku dostępnych jest wiele różnych rodzajów smarów, które różnią się składem chemicznym oraz właściwościami fizycznymi. Najczęściej stosowane są oleje mineralne oraz syntetyczne, które charakteryzują się dobrą lepkością oraz odpornością na wysokie temperatury. Oleje mineralne są często tańsze i łatwiejsze w dostępności, jednak mogą nie zapewniać takiej samej wydajności jak oleje syntetyczne, które oferują lepszą ochronę przed zużyciem oraz korozją. Istnieją także specjalistyczne smary teflonowe lub grafitowe, które są przeznaczone do szczególnie wymagających aplikacji i oferują doskonałe właściwości ślizgowe. Ważne jest również zwrócenie uwagi na dodatki zawarte w danym smarze – niektóre z nich mogą zawierać substancje przeciwdziałające utlenianiu czy korozji, co dodatkowo zwiększa ich skuteczność.
Jakie są najlepsze praktyki dotyczące przechowywania narzędzi pneumatycznych po ich użyciu
Prawidłowe przechowywanie narzędzi pneumatycznych po ich użyciu ma ogromne znaczenie dla zachowania ich sprawności oraz wydajności przez długi czas. Po zakończeniu pracy warto dokładnie oczyścić narzędzie z wszelkich zanieczyszczeń oraz resztek materiałów eksploatacyjnych. W przypadku narzędzi pneumatycznych ważne jest również odłączenie ich od źródła zasilania oraz powietrza, co zapobiega przypadkowemu uruchomieniu urządzenia podczas transportu lub przechowywania. Narzędzia powinny być przechowywane w suchym miejscu o stabilnej temperaturze, z dala od wilgoci oraz ekstremalnych warunków atmosferycznych, które mogą prowadzić do korozji lub uszkodzeń mechanicznych. Dobrą praktyką jest także umieszczanie narzędzi w dedykowanych futerałach lub skrzyniach warsztatowych, co chroni je przed przypadkowymi uderzeniami czy zarysowaniami.
Jakie są najważniejsze zasady bezpieczeństwa przy pracy z narzędziami pneumatycznymi
Praca z narzędziami pneumatycznymi wiąże się z pewnym ryzykiem, dlatego ważne jest przestrzeganie zasad bezpieczeństwa podczas ich użytkowania. Przed rozpoczęciem pracy należy zawsze zapoznać się z instrukcją obsługi danego urządzenia oraz zwrócić uwagę na zalecenia producenta dotyczące jego użytkowania i konserwacji. Użytkownicy powinni nosić odpowiednią odzież ochronną, taką jak rękawice robocze czy okulary ochronne, aby minimalizować ryzyko urazów związanych z odpryskami materiału lub przypadkowymi kontaktami ze sprzętem. Należy również upewnić się, że miejsce pracy jest dobrze oświetlone i wolne od przeszkód mogących utrudniać swobodne poruszanie się podczas korzystania z narzędzi pneumatycznych. Ważnym aspektem jest także regularna kontrola stanu technicznego sprzętu – wszelkie uszkodzenia lub nieszczelności powinny być natychmiast naprawiane przed dalszym użytkowaniem urządzenia.