Fabryka przyszłości 4.0
Fabryka przyszłości 4.0 to koncepcja, która odnosi się do nowoczesnych technologii w produkcji, integrujących zaawansowane systemy informatyczne z procesami wytwórczymi. W sercu tej idei leży Internet Rzeczy, który umożliwia komunikację między maszynami, czujnikami oraz systemami zarządzania. Dzięki temu możliwe jest zbieranie danych w czasie rzeczywistym, co pozwala na optymalizację procesów produkcyjnych oraz zwiększenie efektywności. W fabrykach 4.0 kluczową rolę odgrywają również sztuczna inteligencja i uczenie maszynowe, które pomagają w analizie zebranych danych oraz przewidywaniu awarii maszyn. To podejście prowadzi do większej elastyczności produkcji, co jest niezbędne w dzisiejszym dynamicznie zmieniającym się rynku. Fabryki przyszłości są również bardziej zrównoważone ekologicznie, dzięki zastosowaniu technologii minimalizujących odpady i zużycie energii.
Jakie technologie są wykorzystywane w fabrykach 4.0
W fabrykach przyszłości 4.0 wykorzystywane są różnorodne technologie, które wspierają automatyzację i cyfryzację procesów produkcyjnych. Kluczowym elementem jest Internet Rzeczy, który umożliwia połączenie maszyn i urządzeń w sieci, co pozwala na zbieranie i analizowanie danych na bieżąco. Kolejną istotną technologią jest sztuczna inteligencja, która pozwala na przetwarzanie dużych zbiorów danych oraz podejmowanie decyzji w oparciu o algorytmy uczenia maszynowego. Robotyka również odgrywa znaczącą rolę w fabrykach 4.0, gdzie roboty współpracujące z ludźmi wykonują powtarzalne zadania, zwiększając wydajność i bezpieczeństwo pracy. Dodatkowo technologia druku 3D staje się coraz bardziej popularna, umożliwiając szybkie prototypowanie oraz produkcję części na żądanie.
Jakie korzyści przynosi wdrożenie fabryk przyszłości 4.0
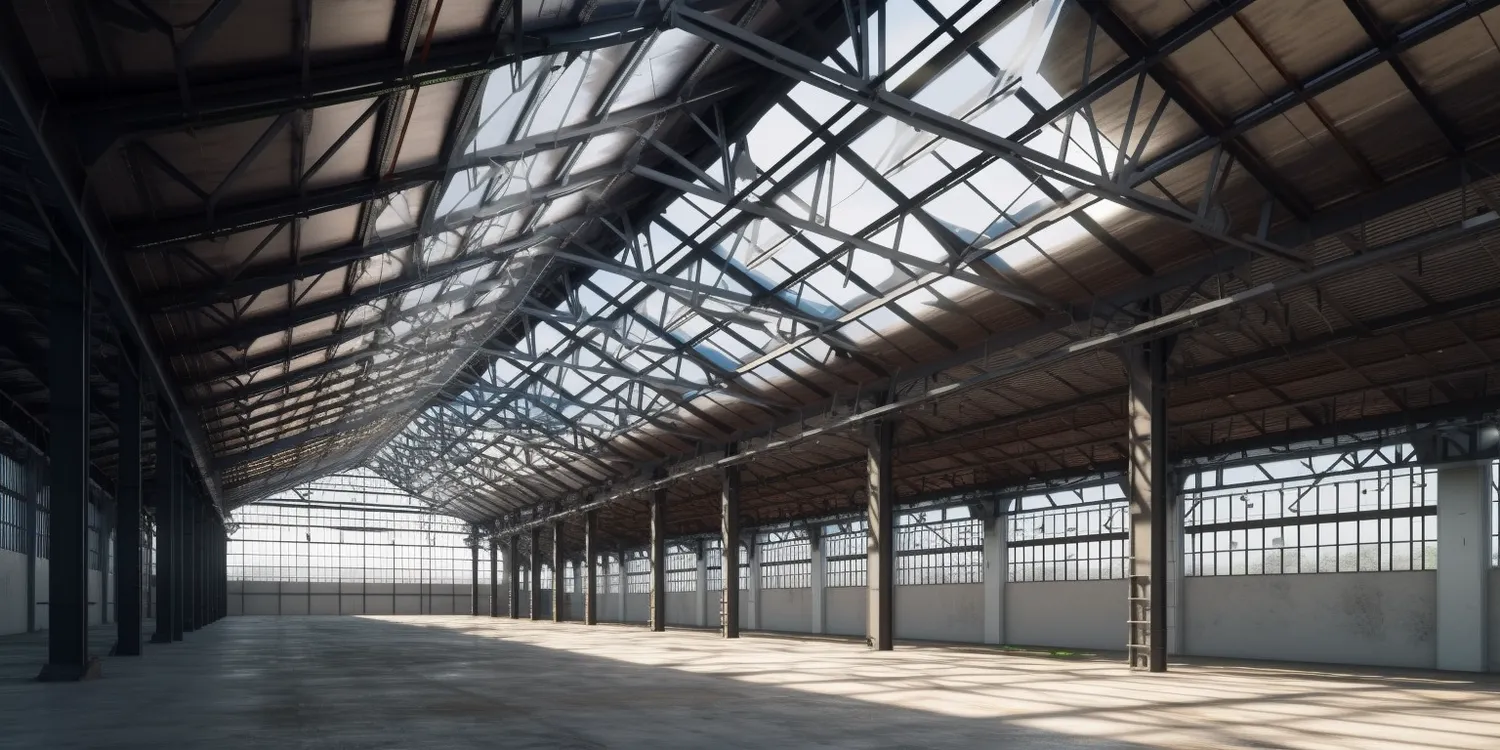
Wdrożenie koncepcji fabryki przyszłości 4.0 niesie ze sobą szereg korzyści dla przedsiębiorstw oraz ich pracowników. Przede wszystkim zwiększa efektywność procesów produkcyjnych poprzez automatyzację rutynowych zadań oraz optymalizację wykorzystania zasobów. Dzięki zbieraniu danych w czasie rzeczywistym możliwe jest szybsze podejmowanie decyzji oraz reagowanie na zmiany w otoczeniu rynkowym. Fabryki 4.0 przyczyniają się także do poprawy jakości produktów poprzez zastosowanie zaawansowanych systemów monitorowania i kontroli jakości na każdym etapie produkcji. Zmniejszenie ilości odpadów i lepsze zarządzanie energią przekładają się na niższe koszty operacyjne oraz mniejszy wpływ na środowisko naturalne. Warto również zauważyć, że wdrożenie nowoczesnych technologii sprzyja innowacyjności i rozwojowi kompetencji pracowników, co może prowadzić do większego zaangażowania zespołu oraz poprawy atmosfery pracy.
Jakie wyzwania stoją przed firmami wdrażającymi fabryki 4.0
Wdrażanie koncepcji fabryki przyszłości 4.0 wiąże się z wieloma wyzwaniami, które przedsiębiorstwa muszą pokonać, aby skutecznie zrealizować swoje cele związane z cyfryzacją i automatyzacją produkcji. Jednym z głównych problemów jest wysoki koszt inwestycji w nowoczesne technologie oraz infrastrukturę IT, co może stanowić barierę dla wielu firm, zwłaszcza małych i średnich przedsiębiorstw. Kolejnym wyzwaniem jest konieczność przeszkolenia pracowników w zakresie obsługi nowych systemów oraz technologii, co wymaga czasu i zasobów finansowych. Dodatkowo wiele organizacji boryka się z problemem integracji istniejących systemów z nowymi rozwiązaniami technologicznymi, co może prowadzić do opóźnień w realizacji projektów. Warto także zwrócić uwagę na kwestie związane z bezpieczeństwem danych oraz ochroną prywatności użytkowników, które stają się coraz ważniejsze w erze cyfrowej transformacji.
Jakie są przykłady fabryk przyszłości 4.0 w praktyce
Wiele firm na całym świecie wdraża koncepcję fabryki przyszłości 4.0, co pozwala na obserwację różnorodnych przykładów zastosowania nowoczesnych technologii w praktyce. Na przykład, niemiecka firma Siemens zrealizowała projekt w swojej fabryce w Amberg, gdzie zastosowano zaawansowane systemy automatyzacji oraz Internet Rzeczy. Dzięki tym rozwiązaniom możliwe jest monitorowanie produkcji w czasie rzeczywistym oraz szybkie reagowanie na wszelkie nieprawidłowości. Inny przykład to firma General Electric, która wdrożyła platformę Predix, umożliwiającą analizę danych z maszyn przemysłowych i przewidywanie awarii jeszcze przed ich wystąpieniem. W Polsce również można znaleźć przykłady fabryk 4.0, takie jak zakład produkcyjny firmy KGHM, który wykorzystuje nowoczesne technologie do zarządzania procesami wydobywczymi oraz przetwórczymi. Takie innowacyjne podejście pozwala na zwiększenie efektywności operacyjnej oraz redukcję kosztów, co jest kluczowe w konkurencyjnym środowisku rynkowym.
Jakie umiejętności są potrzebne w fabrykach przyszłości 4.0
W kontekście fabryk przyszłości 4.0 niezwykle istotne staje się posiadanie odpowiednich umiejętności przez pracowników, aby mogli efektywnie funkcjonować w zautomatyzowanym i cyfrowym środowisku pracy. Przede wszystkim niezbędna jest znajomość technologii informacyjnych oraz umiejętność obsługi nowoczesnych narzędzi i systemów, takich jak oprogramowanie do analizy danych czy platformy chmurowe. Ponadto, umiejętności związane z programowaniem oraz inżynierią danych stają się coraz bardziej pożądane, ponieważ umożliwiają pracownikom lepsze zrozumienie i wykorzystanie możliwości oferowanych przez sztuczną inteligencję i uczenie maszynowe. Warto również zwrócić uwagę na znaczenie kompetencji interpersonalnych, takich jak zdolność do pracy zespołowej oraz komunikacji, które są kluczowe w środowisku opartym na współpracy między ludźmi a maszynami. Dodatkowo elastyczność i gotowość do nauki nowych umiejętności są niezwykle ważne w obliczu dynamicznych zmian technologicznych.
Jak wpływa fabryka przyszłości 4.0 na rynek pracy
Wprowadzenie koncepcji fabryki przyszłości 4.0 ma istotny wpływ na rynek pracy, który przechodzi znaczące zmiany związane z automatyzacją i cyfryzacją procesów produkcyjnych. Z jednej strony wiele tradycyjnych stanowisk może zostać zredukowanych lub całkowicie wyeliminowanych w wyniku zastąpienia ludzi przez maszyny i roboty. Z drugiej strony jednak pojawiają się nowe miejsca pracy wymagające specjalistycznych umiejętności związanych z technologią i innowacjami. Pracownicy muszą dostosować się do zmieniających się wymagań rynku pracy, co często wiąże się z koniecznością zdobywania nowych kwalifikacji oraz ciągłego kształcenia się. Warto zauważyć, że fabryki 4.0 mogą przyczynić się do poprawy warunków pracy poprzez zwiększenie bezpieczeństwa i ergonomii stanowisk pracy dzięki zastosowaniu nowoczesnych technologii oraz automatyzacji rutynowych zadań.
Jakie są trendy rozwoju fabryk przyszłości 4.0
Trendy rozwoju fabryk przyszłości 4.0 wskazują na dalszą ewolucję technologii oraz ich integrację z procesami produkcyjnymi. Jednym z najważniejszych trendów jest rozwój sztucznej inteligencji i uczenia maszynowego, które będą coraz bardziej wykorzystywane do analizy danych oraz optymalizacji procesów produkcyjnych. W miarę jak technologia będzie się rozwijać, możliwe stanie się jeszcze skuteczniejsze przewidywanie awarii maszyn oraz dostosowywanie produkcji do zmieniających się potrzeb rynku. Kolejnym istotnym trendem jest rosnąca popularność rozwiązań opartych na chmurze obliczeniowej, które umożliwiają łatwe przechowywanie i udostępnianie danych oraz aplikacji między różnymi działami firmy. Warto także zwrócić uwagę na rozwój technologii blockchain, która może przyczynić się do zwiększenia transparentności i bezpieczeństwa procesów produkcyjnych poprzez umożliwienie śledzenia pochodzenia surowców oraz historii produktów.
Jakie są różnice między tradycyjnymi a nowoczesnymi fabrykami 4.0
Różnice między tradycyjnymi a nowoczesnymi fabrykami 4.0 są znaczące i dotyczą wielu aspektów funkcjonowania przedsiębiorstw produkcyjnych. Tradycyjne fabryki często opierają się na manualnych procesach produkcyjnych oraz ograniczonej automatyzacji, co prowadzi do większej liczby błędów ludzkich oraz niższej efektywności operacyjnej. W przeciwieństwie do nich fabryki 4.0 korzystają z zaawansowanych technologii takich jak Internet Rzeczy, sztuczna inteligencja czy robotyka współpracująca, co pozwala na automatyzację wielu procesów oraz zbieranie danych w czasie rzeczywistym. Kolejną różnicą jest podejście do zarządzania danymi – nowoczesne fabryki stawiają na analizę dużych zbiorów danych (big data) oraz ich wykorzystanie do podejmowania decyzji strategicznych, podczas gdy tradycyjne metody opierają się głównie na doświadczeniu menedżerów i intuicji.
Jakie wyzwania związane są z cyberbezpieczeństwem w fabrykach 4.0
Cyberbezpieczeństwo stanowi jedno z kluczowych wyzwań dla fabryk przyszłości 4.0 ze względu na rosnącą liczbę połączeń między urządzeniami oraz systemami informatycznymi w ramach Internetu Rzeczy. W miarę jak coraz więcej urządzeń jest podłączonych do sieci, ryzyko ataków hakerskich wzrasta, co może prowadzić do poważnych konsekwencji dla przedsiębiorstw, takich jak utrata danych czy przerwy w produkcji. Firmy muszą inwestować w odpowiednie zabezpieczenia systemów informatycznych oraz edukować swoich pracowników o zagrożeniach związanych z cyberatakami i sposobach ich unikania. Kluczowym elementem strategii bezpieczeństwa powinno być regularne aktualizowanie oprogramowania oraz stosowanie zaawansowanych metod szyfrowania danych, które mogą pomóc w ochronie przed nieautoryzowanym dostępem do informacji krytycznych dla działalności firmy.