Destylator przemysłowy
Destylator przemysłowy to urządzenie, które służy do rozdzielania cieczy na podstawie różnicy w temperaturze wrzenia. Proces ten jest kluczowy w wielu branżach, takich jak chemiczna, petrochemiczna czy spożywcza. Działanie destylatora opiera się na podgrzewaniu cieczy, co powoduje jej parowanie. Opary następnie są schładzane i kondensowane z powrotem do postaci cieczy. W ten sposób można oddzielić substancje o różnych temperaturach wrzenia, co pozwala na uzyskanie czystszych frakcji. W przemyśle często stosuje się różne typy destylatorów, takie jak destylatory prostokątne, kolumnowe czy wirówkowe, które różnią się konstrukcją oraz zastosowaniem. Wybór odpowiedniego typu destylatora zależy od specyfiki procesu oraz rodzaju przetwarzanych substancji. Warto również zauważyć, że w procesie destylacji mogą występować różne zjawiska, takie jak azeotropowość, która wpływa na efektywność rozdzielania składników.
Jakie są zastosowania destylatorów przemysłowych w różnych branżach
Destylatory przemysłowe znajdują szerokie zastosowanie w różnych sektorach gospodarki. W przemyśle chemicznym są wykorzystywane do produkcji rozpuszczalników, kwasów oraz innych substancji chemicznych. Proces destylacji pozwala na uzyskanie czystych frakcji, które są niezbędne do dalszej obróbki lub jako gotowe produkty. W branży petrochemicznej destylatory służą do separacji ropy naftowej na poszczególne frakcje, takie jak benzyna, olej napędowy czy nafta. Dzięki temu możliwe jest uzyskanie paliw o różnych właściwościach i zastosowaniach. W przemyśle spożywczym destylatory są używane do produkcji alkoholi oraz ekstraktów smakowych. Na przykład w produkcji whisky czy wina proces destylacji jest kluczowym etapem, który wpływa na smak i aromat końcowego produktu. Ponadto destylatory znajdują zastosowanie w laboratoriach badawczych, gdzie służą do oczyszczania próbek oraz analizy składu chemicznego substancji.
Jakie są najważniejsze rodzaje destylatorów przemysłowych dostępnych na rynku
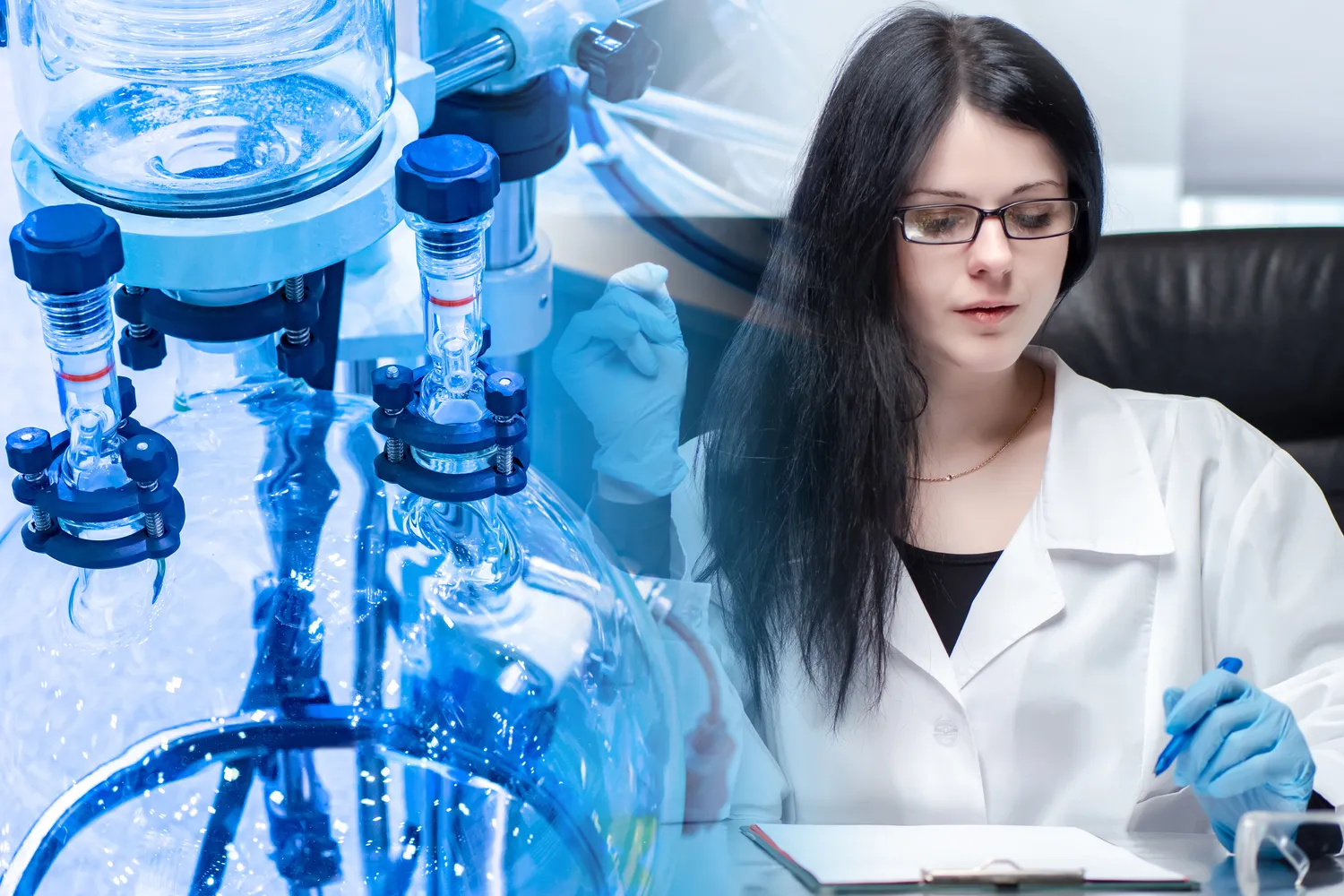
Na rynku dostępnych jest wiele rodzajów destylatorów przemysłowych, które różnią się zarówno konstrukcją, jak i przeznaczeniem. Jednym z najpopularniejszych typów jest destylator kolumnowy, który charakteryzuje się dużą efektywnością separacji dzięki zastosowaniu kolumny z wypełnieniem lub talerzami. Tego typu urządzenia są często wykorzystywane w przemyśle petrochemicznym oraz chemicznym do rozdzielania składników o zbliżonych temperaturach wrzenia. Innym ważnym rodzajem jest destylator prostokątny, który znajduje zastosowanie głównie w procesach wymagających mniejszych ilości surowców. Destylatory wirówkowe natomiast wykorzystują siłę odśrodkową do separacji cieczy i są szczególnie przydatne w przypadku emulsji oraz zawiesin. Warto również wspomnieć o destylatorach laboratoryjnych, które służą do przeprowadzania eksperymentów oraz analiz chemicznych w mniejszych skalach.
Jakie są kluczowe czynniki wpływające na wydajność destylacji
Wydajność procesu destylacji zależy od wielu czynników, które mogą znacząco wpłynąć na jakość uzyskiwanych frakcji oraz efektywność całego procesu. Jednym z najważniejszych aspektów jest temperatura podgrzewania cieczy, która musi być odpowiednio dobrana do rodzaju przetwarzanych substancji. Zbyt wysoka temperatura może prowadzić do niepożądanych reakcji chemicznych lub degradacji składników, podczas gdy zbyt niska może skutkować niewystarczającą separacją frakcji. Kolejnym istotnym czynnikiem jest czas trwania procesu destylacji; im dłużej trwa proces, tym większa szansa na uzyskanie czystszych frakcji. Również konstrukcja samego urządzenia ma kluczowe znaczenie; odpowiednio zaprojektowane kolumny czy wymienniki ciepła mogą znacznie poprawić efektywność separacji. Oprócz tego warto zwrócić uwagę na jakość surowców wejściowych oraz ich skład chemiczny, ponieważ obecność zanieczyszczeń może negatywnie wpłynąć na rezultaty procesu.
Jakie są najczęstsze problemy związane z destylatorami przemysłowymi
W trakcie eksploatacji destylatorów przemysłowych mogą wystąpić różne problemy, które wpływają na ich wydajność oraz jakość uzyskiwanych produktów. Jednym z najczęstszych problemów jest zatykanie kolumny destylacyjnej, co może być spowodowane osadzaniem się zanieczyszczeń lub nieodpowiednich substancji chemicznych. Zatykanie prowadzi do obniżenia efektywności separacji i może wymagać czasochłonnych prac konserwacyjnych. Innym istotnym problemem jest niewłaściwe ustawienie parametrów procesu, takich jak temperatura czy ciśnienie, co może prowadzić do nieefektywnej destylacji oraz uzyskiwania frakcji o nieodpowiedniej czystości. W przypadku destylatorów wirówkowych często występują problemy związane z równomiernym rozkładem cieczy w wirniku, co wpływa na efektywność separacji. Dodatkowo, w przypadku długotrwałej eksploatacji urządzeń mogą wystąpić problemy związane z korozją lub zużyciem materiałów, co również wpływa na ich wydajność i trwałość.
Jakie są nowoczesne technologie w dziedzinie destylacji przemysłowej
W ostatnich latach w dziedzinie destylacji przemysłowej pojawiły się nowoczesne technologie, które znacząco poprawiają efektywność procesów oraz jakość uzyskiwanych produktów. Jedną z innowacyjnych metod jest destylacja membranowa, która wykorzystuje specjalne membrany do separacji składników na podstawie ich wielkości cząsteczkowej. Ta technologia pozwala na osiągnięcie wysokiej czystości produktów przy niższych kosztach energetycznych w porównaniu do tradycyjnych metod. Kolejnym przykładem nowoczesnej technologii jest destylacja podciśnieniowa, która umożliwia przeprowadzanie procesów w obniżonym ciśnieniu. Dzięki temu można destylować substancje w niższych temperaturach, co minimalizuje ryzyko degradacji termicznej. Warto również wspomnieć o zastosowaniu sztucznej inteligencji i analizy danych w optymalizacji procesów destylacyjnych. Dzięki zaawansowanym algorytmom możliwe jest monitorowanie parametrów pracy urządzeń oraz automatyczne dostosowywanie ich do zmieniających się warunków, co zwiększa wydajność i jakość produkcji.
Jakie są koszty inwestycji w destylatory przemysłowe
Koszty inwestycji w destylatory przemysłowe mogą być znaczne i zależą od wielu czynników, takich jak typ urządzenia, jego wydajność oraz dodatkowe funkcje. Na początku należy uwzględnić koszty zakupu samego urządzenia, które mogą sięgać od kilku tysięcy do nawet milionów złotych w przypadku dużych instalacji przemysłowych. Oprócz kosztu zakupu warto również brać pod uwagę koszty instalacji oraz uruchomienia urządzenia, które mogą obejmować prace budowlane, elektryczne oraz hydrauliczne. Koszty eksploatacyjne to kolejny ważny aspekt; obejmują one zużycie energii, konserwację oraz ewentualne naprawy. Warto również pamiętać o kosztach związanych z surowcami oraz materiałami eksploatacyjnymi, które mogą mieć znaczący wpływ na rentowność całego procesu.
Jakie są kluczowe aspekty bezpieczeństwa przy pracy z destylatorami przemysłowymi
Bezpieczeństwo pracy z destylatorami przemysłowymi jest niezwykle istotnym zagadnieniem, które powinno być priorytetem dla każdego zakładu produkcyjnego. Praca z substancjami chemicznymi wiąże się z różnymi zagrożeniami, takimi jak wybuchy, pożary czy kontakt ze szkodliwymi oparami. Dlatego kluczowym aspektem jest odpowiednie szkolenie pracowników dotyczące obsługi urządzeń oraz procedur bezpieczeństwa. Ważne jest również stosowanie odpowiednich środków ochrony osobistej, takich jak rękawice, gogle czy maski ochronne, aby minimalizować ryzyko narażenia na niebezpieczne substancje. Kolejnym istotnym elementem jest regularna konserwacja urządzeń oraz kontrola ich stanu technicznego; wszelkie usterki powinny być natychmiast naprawiane, aby uniknąć poważniejszych incydentów. Systemy wentylacyjne oraz detektory gazu powinny być standardem w każdym zakładzie zajmującym się destylacją, aby zapewnić odpowiednią cyrkulację powietrza i wykrywanie potencjalnych zagrożeń.
Jakie są przyszłe kierunki rozwoju technologii destylacyjnej
Przyszłość technologii destylacyjnej zapowiada się obiecująco dzięki ciągłemu rozwojowi innowacyjnych rozwiązań oraz rosnącemu naciskowi na zrównoważony rozwój. W miarę jak przemysł staje przed wyzwaniami związanymi ze zmianami klimatycznymi i ograniczonymi zasobami naturalnymi, poszukiwanie bardziej efektywnych i ekologicznych metod produkcji staje się kluczowe. Jednym z kierunków rozwoju jest integracja systemów destylacyjnych z odnawialnymi źródłami energii, co pozwoli na zmniejszenie zużycia energii oraz emisji gazów cieplarnianych. Ponadto rozwijają się technologie związane z recyklingiem i ponownym wykorzystaniem surowców, co przyczynia się do bardziej efektywnego zarządzania zasobami i ograniczenia odpadów. Również automatyzacja procesów oraz zastosowanie sztucznej inteligencji będą miały coraz większe znaczenie; inteligentne systemy zarządzania mogą optymalizować parametry pracy urządzeń w czasie rzeczywistym, co zwiększa wydajność i jakość produkcji.
Jakie są najważniejsze kryteria wyboru destylatora przemysłowego
Wybór odpowiedniego destylatora przemysłowego jest kluczowym krokiem w procesie produkcyjnym, który może znacząco wpłynąć na efektywność i jakość uzyskiwanych produktów. Pierwszym kryterium, które należy wziąć pod uwagę, jest rodzaj przetwarzanych substancji oraz ich właściwości fizykochemiczne. Różne typy destylatorów są przeznaczone do różnych zastosowań, dlatego ważne jest, aby dobrać urządzenie odpowiednie do specyfiki procesu. Kolejnym istotnym aspektem jest wydajność destylatora, która powinna być dostosowana do potrzeb produkcyjnych zakładu. Warto również zwrócić uwagę na koszty eksploatacyjne, takie jak zużycie energii oraz konserwacja urządzenia. Dodatkowo, dostępność części zamiennych oraz wsparcie techniczne producenta mogą mieć duże znaczenie w dłuższej perspektywie czasowej. Ostatnim, ale nie mniej ważnym kryterium jest zgodność z normami bezpieczeństwa oraz ekologicznymi, co pozwala na zapewnienie bezpiecznej i zrównoważonej produkcji.