Destylator laboratoryjny
Destylator laboratoryjny to urządzenie, które służy do oddzielania substancji na podstawie różnicy w ich temperaturach wrzenia. Proces ten jest kluczowy w wielu dziedzinach nauki, takich jak chemia, biochemia czy farmacja. W laboratoriach destylatory są wykorzystywane do oczyszczania cieczy, odzyskiwania rozpuszczalników oraz przygotowywania różnych roztworów. W praktyce destylacja polega na podgrzewaniu cieczy do momentu, gdy zaczyna parować, a następnie schładzaniu pary, aby skondensować ją z powrotem do stanu ciekłego. Dzięki temu możliwe jest oddzielenie substancji o różnych właściwościach fizycznych. W laboratoriach często stosuje się różne rodzaje destylatorów, w tym destylatory prostokątne, frakcyjne oraz rotacyjne, które różnią się budową i przeznaczeniem. Warto również zaznaczyć, że proces destylacji może być stosowany nie tylko w celach badawczych, ale także przemysłowych, gdzie wykorzystywany jest do produkcji alkoholi czy oczyszczania wody.
Jakie są rodzaje destylatorów laboratoryjnych i ich charakterystyka
W laboratoriach można spotkać różne typy destylatorów, które są dostosowane do specyficznych potrzeb użytkowników. Najpopularniejszym rodzajem jest destylator prosty, który składa się z kolby grzewczej, chłodnicy i zbiornika na skropliny. Tego typu urządzenie jest idealne do podstawowych procesów destylacji, zwłaszcza gdy chcemy oddzielić substancje o znacznej różnicy temperatur wrzenia. Kolejnym typem jest destylator frakcyjny, który wyposażony jest w kolumnę frakcyjną. Umożliwia on bardziej skomplikowane procesy separacji, co jest szczególnie przydatne w przypadku mieszanin zawierających wiele składników o zbliżonych temperaturach wrzenia. Destylatory rotacyjne to kolejna kategoria urządzeń, które umożliwiają przeprowadzanie destylacji w warunkach niskiego ciśnienia, co pozwala na efektywne oddzielanie substancji termolabilnych. Każdy z tych typów ma swoje unikalne cechy i zastosowania, co sprawia, że wybór odpowiedniego destylatora zależy od specyfiki przeprowadzanych badań oraz wymagań dotyczących jakości uzyskiwanych produktów.
Jakie są kluczowe elementy budowy destylatora laboratoryjnego
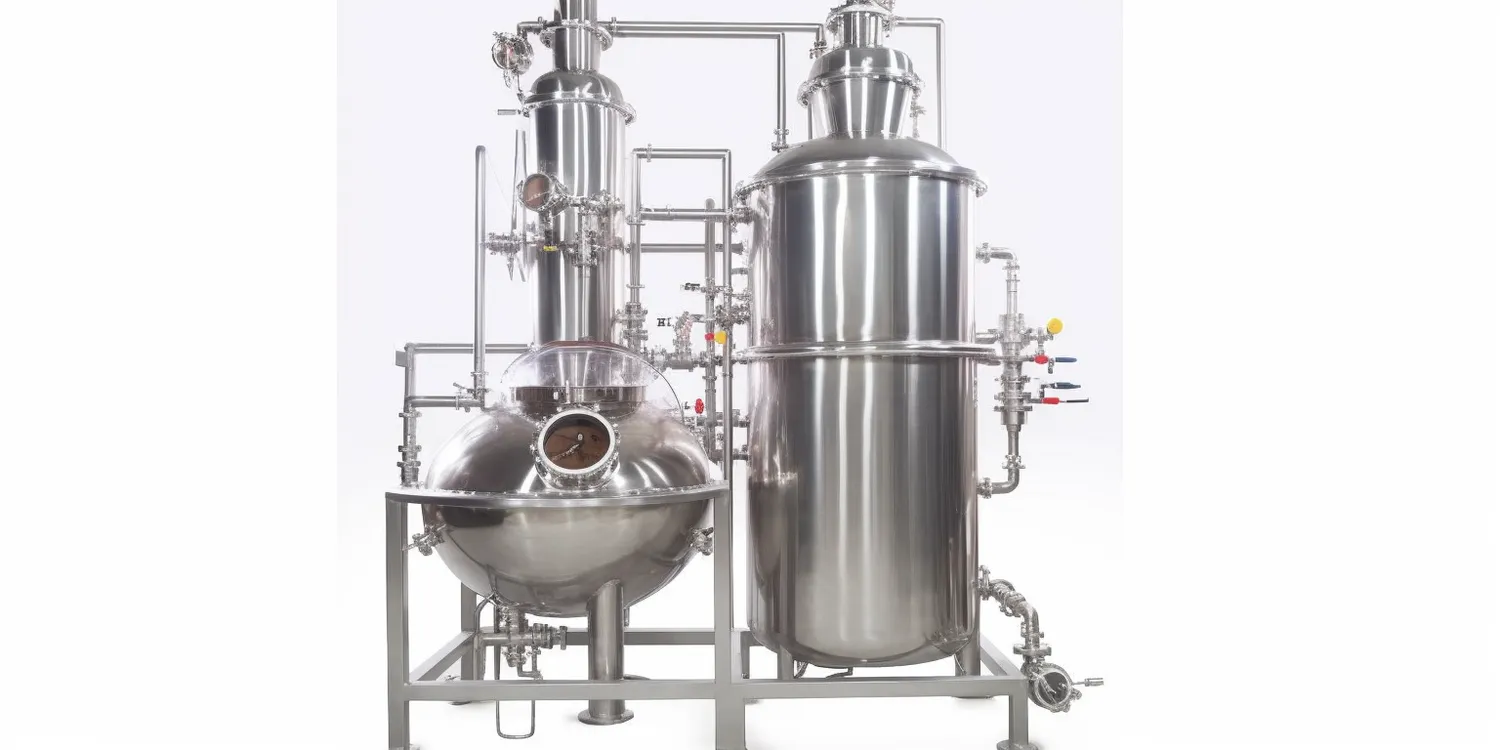
Budowa destylatora laboratoryjnego opiera się na kilku kluczowych elementach, które współdziałają ze sobą podczas procesu destylacji. Podstawowym komponentem jest kolba grzewcza, która służy do podgrzewania cieczy do momentu jej wrzenia. Kolba ta wykonana jest zazwyczaj ze szkła borokrzemowego, co zapewnia wysoką odporność na zmiany temperatury oraz chemikalia. Drugim istotnym elementem jest chłodnica, która ma za zadanie schłodzić pary wydobywające się z kolby grzewczej i skondensować je z powrotem do stanu ciekłego. Chłodnice mogą mieć różne formy – najczęściej spotykane to chłodnice Liebiga oraz chłodnice typu Allihn. Kolejnym ważnym elementem jest zbiornik na skropliny, który gromadzi oczyszczoną ciecz po procesie destylacji. Warto również zwrócić uwagę na elementy dodatkowe, takie jak termometry czy manometry, które umożliwiają monitorowanie warunków panujących podczas procesu oraz zapewniają większą kontrolę nad przebiegiem eksperymentu.
Jakie materiały są używane do produkcji destylatorów laboratoryjnych
Produkcja destylatorów laboratoryjnych opiera się na materiałach o wysokiej odporności chemicznej i termicznej. Najczęściej wykorzystywanym materiałem jest szkło borokrzemowe, które charakteryzuje się niskim współczynnikiem rozszerzalności cieplnej oraz wysoką odpornością na działanie kwasów i zasad. Szkło borokrzemowe jest idealne do budowy kolb grzewczych oraz chłodnic, ponieważ zapewnia bezpieczeństwo podczas pracy z substancjami chemicznymi oraz umożliwia łatwe obserwowanie zachodzących procesów. W przypadku elementów narażonych na działanie wysokich temperatur lub ciśnienia często stosuje się również stal nierdzewną lub inne metale odporne na korozję. Materiały te są szczególnie ważne w kontekście długotrwałego użytkowania urządzeń laboratoryjnych oraz ich konserwacji. Warto także wspomnieć o uszczelkach i innych komponentach wykonanych z elastomerów czy teflonu, które zapewniają szczelność układu i minimalizują ryzyko wycieków substancji chemicznych.
Jakie są najczęstsze problemy związane z użytkowaniem destylatora laboratoryjnego
Podczas użytkowania destylatora laboratoryjnego mogą wystąpić różnorodne problemy techniczne, które mogą wpłynąć na efektywność procesu destylacji oraz jakość uzyskiwanych produktów. Jednym z najczęstszych problemów jest niewłaściwe ustawienie temperatury grzania, co może prowadzić do niepełnej separacji składników lub ich degradacji. Zbyt wysoka temperatura może spowodować rozkład substancji termolabilnych, natomiast zbyt niska może skutkować brakiem odpowiedniej wydajności procesu. Innym istotnym zagadnieniem są problemy związane z chłodzeniem par – jeśli chłodnica nie działa prawidłowo lub nie jest odpowiednio schładzana wodą, może dojść do kondensacji pary w niewłaściwy sposób lub nawet do ich ucieczki z układu. Nieszczelności w systemie również mogą stanowić poważny problem; mogą prowadzić do utraty cennych substancji lub niebezpiecznych wycieków chemikaliów.
Jakie są kluczowe zasady bezpieczeństwa przy pracy z destylatorem laboratoryjnym
Praca z destylatorem laboratoryjnym wiąże się z pewnym ryzykiem, dlatego niezwykle istotne jest przestrzeganie zasad bezpieczeństwa, aby zminimalizować potencjalne zagrożenia. Przede wszystkim, przed rozpoczęciem pracy należy dokładnie zapoznać się z instrukcją obsługi urządzenia oraz z właściwościami chemicznymi substancji, które będą używane w procesie destylacji. Użytkownicy powinni zawsze nosić odpowiednią odzież ochronną, taką jak fartuchy laboratoryjne, rękawice oraz okulary ochronne, aby zabezpieczyć się przed ewentualnymi oparzeniami czy kontaktami z niebezpiecznymi substancjami. Ważne jest również, aby miejsce pracy było dobrze wentylowane, co pomoże w uniknięciu gromadzenia się szkodliwych par. Należy także zadbać o to, aby wszystkie elementy destylatora były prawidłowo zamocowane i szczelne przed rozpoczęciem procesu. W przypadku wystąpienia jakichkolwiek nieprawidłowości, takich jak wycieki czy nieprawidłowe działanie urządzenia, należy natychmiast przerwać pracę i zgłosić problem odpowiednim osobom.
Jakie są najważniejsze zastosowania destylatorów laboratoryjnych w różnych dziedzinach
Destylatory laboratoryjne mają szerokie zastosowanie w różnych dziedzinach nauki i przemysłu. W chemii organicznej są one wykorzystywane do oczyszczania substancji chemicznych poprzez usuwanie rozpuszczalników lub niepożądanych składników. Dzięki temu możliwe jest uzyskanie czystych reagentów do dalszych badań. W biochemii destylatory służą do izolacji i oczyszczania biomolekuł, takich jak białka czy kwasy nukleinowe, co jest kluczowe dla prowadzenia badań nad ich strukturą i funkcją. W przemyśle farmaceutycznym destylacja jest stosowana do produkcji leków oraz ich składników aktywnych, a także do oczyszczania surowców chemicznych wykorzystywanych w produkcji farmaceutyków. Destylatory znajdują również zastosowanie w przemyśle spożywczym, gdzie są używane do produkcji alkoholi oraz ekstraktów roślinnych. W ostatnich latach rośnie zainteresowanie wykorzystaniem destylacji w procesach ekologicznych, takich jak odzyskiwanie rozpuszczalników czy oczyszczanie wody.
Jakie nowoczesne technologie wpływają na rozwój destylatorów laboratoryjnych
W ostatnich latach rozwój technologii znacząco wpłynął na konstrukcję i funkcjonalność destylatorów laboratoryjnych. Nowoczesne urządzenia są często wyposażone w zaawansowane systemy automatyzacji, które umożliwiają precyzyjne kontrolowanie parametrów procesu destylacji, takich jak temperatura czy ciśnienie. Dzięki temu użytkownicy mogą osiągać lepsze wyniki oraz zwiększać wydajność pracy. Wprowadzenie technologii cyfrowych pozwala na monitorowanie przebiegu procesu w czasie rzeczywistym oraz na zbieranie danych do późniejszej analizy. Ponadto nowoczesne materiały wykorzystywane do produkcji destylatorów charakteryzują się lepszą odpornością na działanie chemikaliów oraz wysokich temperatur, co zwiększa trwałość urządzeń i ich bezpieczeństwo użytkowania. Coraz częściej stosuje się także technologie związane z recyklingiem energii, co pozwala na zmniejszenie kosztów eksploatacji oraz wpływu na środowisko. Innowacyjne rozwiązania w zakresie konstrukcji chłodnic czy kolumn frakcyjnych przyczyniają się do poprawy efektywności procesów separacyjnych.
Jakie są koszty zakupu i eksploatacji destylatora laboratoryjnego
Koszty zakupu i eksploatacji destylatora laboratoryjnego mogą się znacznie różnić w zależności od jego typu, producenta oraz specyfikacji technicznych. Podstawowe modele destylatorów prostych można nabyć już za kilka tysięcy złotych, jednak bardziej zaawansowane urządzenia frakcyjne czy rotacyjne mogą kosztować znacznie więcej – nawet kilkadziesiąt tysięcy złotych. Oprócz samego zakupu należy również uwzględnić koszty eksploatacji związane z energią elektryczną potrzebną do podgrzewania cieczy oraz wodą wykorzystywaną do chłodzenia par. Dodatkowo warto pamiętać o regularnej konserwacji sprzętu oraz ewentualnych naprawach, które mogą generować dodatkowe wydatki. Koszty materiałów eksploatacyjnych, takich jak uszczelki czy elementy wymienne również powinny być brane pod uwagę przy planowaniu budżetu na użytkowanie destylatora.
Jakie są perspektywy rozwoju technologii związanej z destylatorami laboratoryjnymi
Perspektywy rozwoju technologii związanej z destylatorami laboratoryjnymi wyglądają obiecująco dzięki ciągłym innowacjom w dziedzinie nauki i inżynierii chemicznej. W miarę jak rośnie zapotrzebowanie na czystsze procesy produkcyjne oraz efektywność energetyczną, producenci urządzeń laboratoryjnych będą musieli dostosować swoje produkty do tych wymagań. Można spodziewać się dalszego rozwoju automatyzacji procesów destylacji, co pozwoli na jeszcze większą precyzję oraz oszczędność czasu podczas przeprowadzania eksperymentów. Wprowadzenie sztucznej inteligencji i uczenia maszynowego może pomóc w optymalizacji warunków pracy destylatorów oraz przewidywaniu wyników procesów separacyjnych na podstawie wcześniejszych danych. Również rozwój materiałów kompozytowych o wysokiej odporności chemicznej może przyczynić się do zwiększenia trwałości urządzeń oraz ich efektywności operacyjnej. W kontekście ochrony środowiska można zauważyć rosnące zainteresowanie technologiami związanymi z recyklingiem rozpuszczalników oraz odzyskiwaniem energii cieplnej z procesów przemysłowych.