Destylacja rozpuszczalników
Destylacja rozpuszczalników to proces, który polega na oddzieleniu składników mieszaniny na podstawie różnicy ich temperatur wrzenia. W praktyce oznacza to, że podczas podgrzewania cieczy, składnik o niższej temperaturze wrzenia odparowuje jako pierwszy, a następnie jest skraplany i zbierany w osobnym naczyniu. Kluczowym elementem tego procesu jest zastosowanie odpowiednich urządzeń, takich jak kolumna destylacyjna, która zwiększa efektywność separacji poprzez wielokrotne skraplanie i parowanie. Warto również zwrócić uwagę na czystość używanych rozpuszczalników oraz na ich właściwości chemiczne, które mogą wpływać na przebieg destylacji. Na przykład, w przypadku rozpuszczalników organicznych, takich jak etanol czy aceton, proces ten może być znacznie bardziej skomplikowany ze względu na ich zdolność do tworzenia azeotropów, co utrudnia uzyskanie czystego produktu.
Jakie są najczęstsze metody destylacji rozpuszczalników
W kontekście destylacji rozpuszczalników wyróżniamy kilka metod, które są stosowane w zależności od charakterystyki substancji oraz pożądanej czystości końcowego produktu. Najpopularniejszą metodą jest destylacja prosta, która polega na jednorazowym podgrzaniu cieczy i zbieraniu pary. Jest to metoda stosunkowo łatwa do przeprowadzenia, jednak ma swoje ograniczenia w przypadku substancji o zbliżonych temperaturach wrzenia. W takich sytuacjach lepszym rozwiązaniem jest destylacja frakcyjna, która wykorzystuje kolumny frakcyjne do lepszego rozdzielenia składników. Kolejną metodą jest destylacja azeotropowa, która pozwala na oddzielenie składników tworzących azeotropy poprzez dodanie odpowiednich substancji pomocniczych. Istnieje także destylacja próżniowa, która obniża ciśnienie atmosferyczne wokół cieczy, co pozwala na obniżenie temperatury wrzenia i minimalizację degradacji termicznej wrażliwych substancji.
Jakie są zastosowania destylacji rozpuszczalników w przemyśle
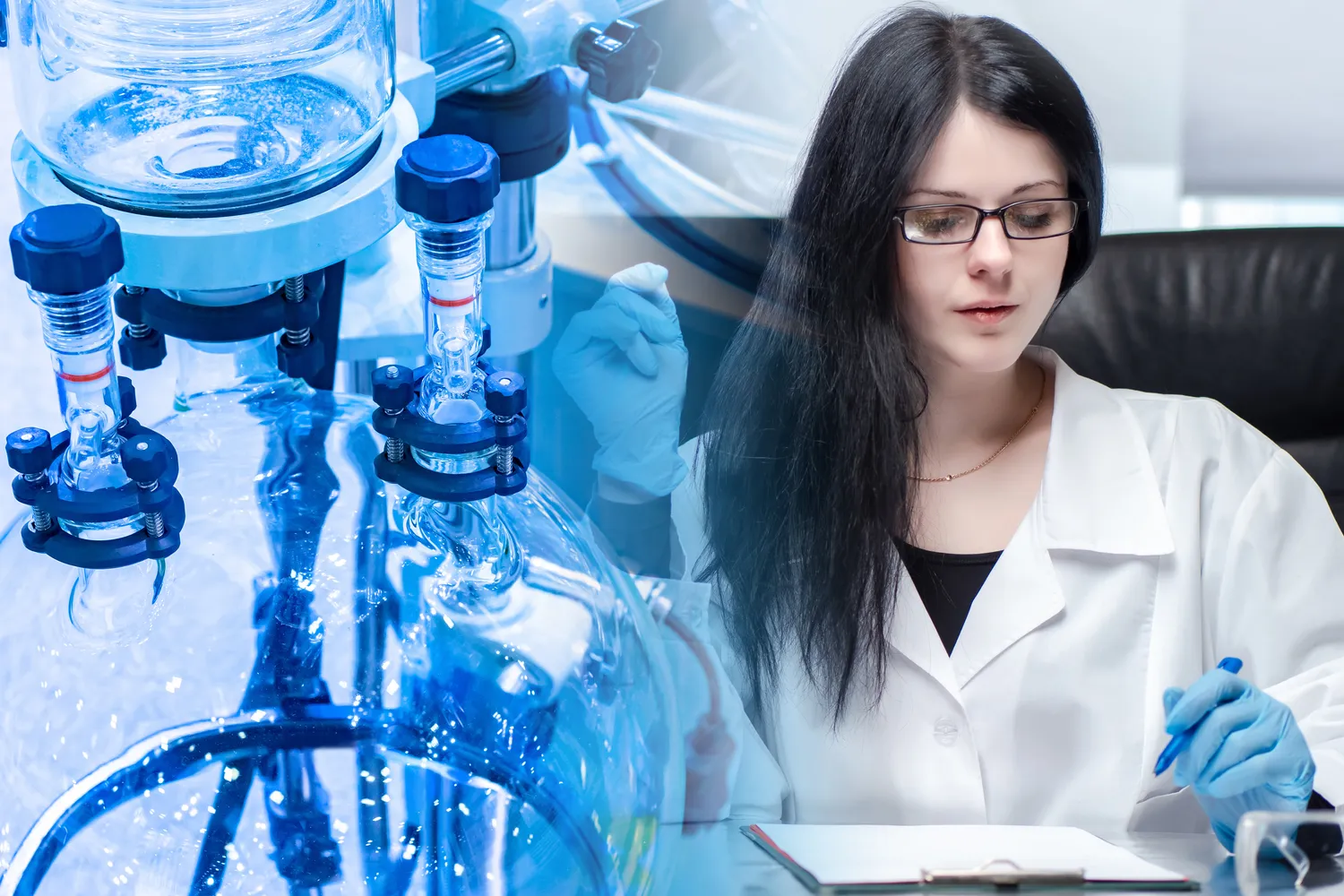
Destylacja rozpuszczalników znajduje szerokie zastosowanie w różnych gałęziach przemysłu chemicznego i farmaceutycznego. W przemyśle chemicznym proces ten jest kluczowy dla oczyszczania surowców oraz produkcji wysokiej jakości chemikaliów. Na przykład, wiele substancji organicznych wymaga destylacji w celu usunięcia zanieczyszczeń lub uzyskania pożądanej czystości. W przemyśle farmaceutycznym destylacja jest niezbędna do produkcji leków oraz ich składników aktywnych, gdzie czystość i jakość są niezwykle istotne. Ponadto, destylacja jest wykorzystywana w produkcji alkoholi oraz olejków eterycznych, gdzie precyzyjne oddzielenie poszczególnych frakcji ma kluczowe znaczenie dla jakości końcowego produktu. W ostatnich latach rośnie również zainteresowanie zastosowaniem destylacji w recyklingu rozpuszczalników, co przyczynia się do zmniejszenia negatywnego wpływu na środowisko oraz oszczędności surowców naturalnych.
Jakie są wyzwania związane z procesem destylacji rozpuszczalników
Pomimo licznych zalet destylacji rozpuszczalników, proces ten wiąże się również z pewnymi wyzwaniami i ograniczeniami. Jednym z głównych problemów jest konieczność precyzyjnego kontrolowania temperatury oraz ciśnienia podczas całego procesu, co może być trudne do osiągnięcia w praktyce przemysłowej. Niewłaściwe ustawienia mogą prowadzić do nieefektywnej separacji lub nawet degradacji cennych składników. Dodatkowo, niektóre mieszaniny mogą tworzyć azeotropy, co utrudnia uzyskanie czystego produktu bez zastosowania dodatkowych substancji pomocniczych lub bardziej skomplikowanych metod separacji. Kolejnym wyzwaniem jest bezpieczeństwo pracy z lotnymi i łatwopalnymi substancjami chemicznymi, które mogą stanowić zagrożenie dla zdrowia pracowników oraz środowiska naturalnego. Dlatego tak ważne jest przestrzeganie odpowiednich norm i procedur bezpieczeństwa podczas prowadzenia procesów destylacyjnych.
Jakie są różnice między destylacją a innymi metodami separacji
Destylacja rozpuszczalników jest jedną z wielu metod separacji składników mieszanin, jednak różni się od innych technik, takich jak ekstrakcja czy filtracja. W przeciwieństwie do filtracji, która polega na oddzielaniu cząstek stałych od cieczy za pomocą porowatych materiałów, destylacja opiera się na różnicy temperatur wrzenia składników. Ekstrakcja natomiast wykorzystuje różnice w rozpuszczalności substancji w różnych rozpuszczalnikach, co może być mniej efektywne w przypadku złożonych mieszanin. Destylacja jest bardziej precyzyjna i pozwala na uzyskanie wyższej czystości produktów, co czyni ją preferowaną metodą w wielu zastosowaniach przemysłowych. Warto również zauważyć, że destylacja może być stosowana w połączeniu z innymi metodami separacji, co zwiększa jej efektywność. Na przykład, w niektórych procesach chemicznych można najpierw zastosować ekstrakcję, a następnie destylację, aby uzyskać jeszcze czystsze frakcje.
Jakie są najnowsze osiągnięcia w technologii destylacji rozpuszczalników
W ostatnich latach technologia destylacji rozpuszczalników uległa znacznym zmianom dzięki postępom w inżynierii chemicznej oraz technologii materiałowej. Nowoczesne kolumny destylacyjne są projektowane z myślą o zwiększonej efektywności energetycznej oraz minimalizacji strat surowców. Wprowadzanie inteligentnych systemów monitorowania i automatyzacji procesów pozwala na dokładniejsze kontrolowanie warunków pracy, co przekłada się na lepszą jakość produktów końcowych. Ponadto, rozwój nowych materiałów do budowy urządzeń destylacyjnych, takich jak nanomateriały czy kompozyty, umożliwia zwiększenie odporności na korozję oraz poprawę wydajności separacji. Warto również wspomnieć o rosnącym zainteresowaniu ekologicznymi metodami destylacji, które mają na celu zmniejszenie zużycia energii oraz emisji gazów cieplarnianych. Przykładem mogą być technologie wykorzystujące energię słoneczną do podgrzewania cieczy w procesie destylacji.
Jakie są kluczowe aspekty bezpieczeństwa przy destylacji rozpuszczalników
Bezpieczeństwo jest jednym z najważniejszych aspektów związanych z procesem destylacji rozpuszczalników, szczególnie gdy pracujemy z substancjami łatwopalnymi i toksycznymi. Kluczowym elementem zapewnienia bezpieczeństwa jest odpowiednie zaprojektowanie i wyposażenie stanowisk pracy. Urządzenia powinny być wykonane z materiałów odpornych na działanie chemikaliów oraz wysokich temperatur. Dodatkowo, systemy wentylacyjne muszą być dostosowane do usuwania potencjalnie niebezpiecznych oparów i gazów. Ważne jest także przestrzeganie procedur awaryjnych oraz regularne szkolenie pracowników w zakresie bezpieczeństwa pracy z substancjami chemicznymi. Należy również pamiętać o stosowaniu odpowiednich środków ochrony osobistej, takich jak rękawice, gogle czy maski ochronne. Regularne przeglądy techniczne urządzeń oraz monitorowanie warunków pracy mogą znacznie zmniejszyć ryzyko wystąpienia niebezpiecznych sytuacji.
Jakie są koszty związane z procesem destylacji rozpuszczalników
Koszty związane z procesem destylacji rozpuszczalników mogą być znaczące i obejmują zarówno wydatki początkowe na zakup sprzętu, jak i bieżące koszty operacyjne. Inwestycje w nowoczesne urządzenia destylacyjne mogą być wysokie, jednak często przekładają się na oszczędności wynikające z większej efektywności energetycznej oraz mniejszych strat surowców. Koszty operacyjne obejmują zużycie energii potrzebnej do podgrzewania cieczy oraz utrzymania odpowiednich warunków pracy. Warto również uwzględnić wydatki związane z konserwacją sprzętu oraz ewentualnymi naprawami. Dodatkowo, jeśli proces wymaga stosowania substancji pomocniczych lub reagentów do poprawy separacji, należy uwzględnić ich koszty w budżecie operacyjnym. W kontekście analizy kosztów warto przeprowadzić dokładną kalkulację opłacalności inwestycji oraz porównać różne metody separacji pod kątem ich efektywności ekonomicznej.
Jakie są przyszłe kierunki rozwoju technologii destylacji rozpuszczalników
Przyszłość technologii destylacji rozpuszczalników zapowiada się obiecująco dzięki ciągłemu postępowi naukowemu i technologicznemu. W miarę jak rośnie zapotrzebowanie na czyste produkty chemiczne oraz ekologiczne metody produkcji, rozwijają się nowe technologie mające na celu zwiększenie efektywności procesów separacyjnych. Jednym z kierunków rozwoju jest integracja procesów chemicznych z technologią destylacyjną, co pozwala na jednoczesne przeprowadzanie reakcji chemicznych i separacji produktów w jednym urządzeniu. Tego rodzaju podejście może znacznie uprościć procesy produkcyjne oraz ograniczyć zużycie energii i surowców. Innym interesującym kierunkiem są badania nad zastosowaniem sztucznej inteligencji i uczenia maszynowego do optymalizacji warunków pracy urządzeń destylacyjnych. Dzięki analizie danych można przewidywać zachowanie mieszanin oraz dostosowywać parametry procesu w czasie rzeczywistym, co zwiększa efektywność produkcji i jakość końcowych produktów.
Jakie są najważniejsze czynniki wpływające na efektywność destylacji rozpuszczalników
Efektywność destylacji rozpuszczalników zależy od wielu czynników, które należy wziąć pod uwagę podczas projektowania i prowadzenia procesu. Kluczowym elementem jest temperatura wrzenia poszczególnych składników mieszaniny, ponieważ różnice te determinują, który składnik odparuje jako pierwszy. Właściwe dobranie temperatury oraz ciśnienia ma ogromny wpływ na wydajność separacji. Kolejnym istotnym czynnikiem jest konstrukcja kolumny destylacyjnej, która powinna być dostosowana do specyfiki przetwarzanej mieszaniny. Wysokość kolumny, liczba teoretycznych płyt czy rodzaj wypełnienia mają znaczenie dla efektywności procesu. Dodatkowo, czas kontaktu pary z cieczą oraz intensywność mieszania mogą wpłynąć na jakość uzyskiwanych frakcji. Ostatecznie, czystość używanych surowców oraz ich właściwości chemiczne również mają kluczowe znaczenie dla sukcesu procesu destylacji.