Budowa maszyn pneumatycznych
Budowa maszyn pneumatycznych opiera się na kilku kluczowych elementach, które współpracują ze sobą w celu efektywnego działania systemu. Podstawowym komponentem jest sprężarka, która ma za zadanie sprężać powietrze i dostarczać je do systemu. Sprężone powietrze jest następnie kierowane do zbiornika, gdzie gromadzi się, co pozwala na stabilne zasilanie pozostałych elementów maszyny. Kolejnym istotnym elementem są zawory, które kontrolują przepływ powietrza w systemie. Dzięki nim można precyzyjnie regulować ciśnienie oraz kierunek przepływu sprężonego powietrza, co jest kluczowe dla prawidłowego funkcjonowania maszyny. Wśród innych ważnych komponentów znajdują się siłowniki pneumatyczne, które przekształcają energię sprężonego powietrza w ruch mechaniczny. Siłowniki te mogą mieć różne kształty i rozmiary, a ich wybór zależy od specyfiki zastosowania. Również nie można zapomnieć o filtrach, które oczyszczają sprężone powietrze z zanieczyszczeń, co jest niezbędne dla długowieczności całego systemu.
Jakie zastosowania mają maszyny pneumatyczne w przemyśle
Maszyny pneumatyczne znajdują szerokie zastosowanie w różnych gałęziach przemysłu, co czyni je niezwykle wszechstronnymi narzędziami. W sektorze produkcyjnym są wykorzystywane do automatyzacji procesów, co pozwala na zwiększenie wydajności i redukcję kosztów pracy. Przykładowo, siłowniki pneumatyczne mogą być stosowane do podnoszenia i przenoszenia ciężkich przedmiotów, co znacznie ułatwia pracę operatorów. W branży motoryzacyjnej maszyny pneumatyczne są używane do montażu części oraz testowania komponentów, gdzie precyzyjne działanie jest kluczowe. W obszarze pakowania i magazynowania również odgrywają istotną rolę, umożliwiając szybkie i efektywne pakowanie produktów oraz ich transport. Dodatkowo w przemyśle spożywczym maszyny pneumatyczne są wykorzystywane do napełniania butelek oraz innych pojemników, co wymaga zachowania wysokich standardów higieny.
Jakie są zalety i wady maszyn pneumatycznych w praktyce
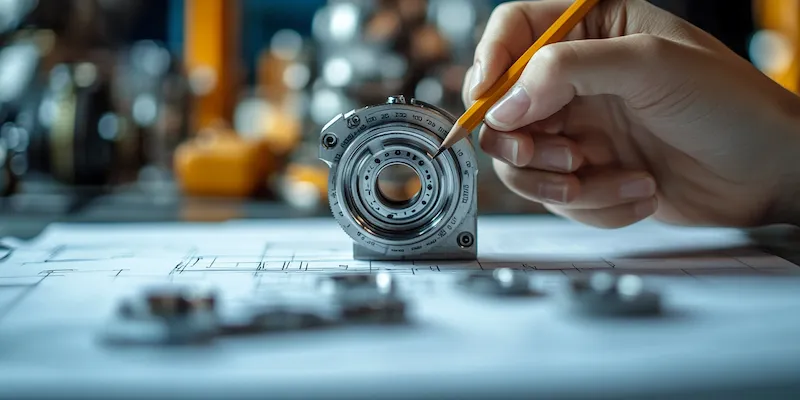
Maszyny pneumatyczne charakteryzują się wieloma zaletami, które sprawiają, że są one chętnie wybierane w różnych zastosowaniach przemysłowych. Jedną z głównych korzyści jest ich prostota konstrukcji oraz łatwość obsługi. Dzięki temu operatorzy mogą szybko nauczyć się ich użytkowania, co przekłada się na krótszy czas szkolenia i szybszą integrację z procesami produkcyjnymi. Ponadto maszyny te są zazwyczaj lżejsze niż ich elektryczne odpowiedniki, co ułatwia ich transport oraz instalację. Warto również zauważyć, że maszyny pneumatyczne są mniej podatne na uszkodzenia związane z przeciążeniem czy przegrzewaniem się silników elektrycznych. Niemniej jednak istnieją także pewne wady związane z ich użytkowaniem. Jednym z głównych problemów jest konieczność dostarczania sprężonego powietrza, co wiąże się z dodatkowymi kosztami związanymi z eksploatacją sprężarek oraz systemów dystrybucji powietrza. Dodatkowo sprężone powietrze może być mniej efektywne w niektórych zastosowaniach wymagających dużej precyzji lub dużych mocy roboczych.
Jakie nowoczesne technologie wspierają budowę maszyn pneumatycznych
W ostatnich latach rozwój technologii znacząco wpłynął na budowę maszyn pneumatycznych oraz ich funkcjonalność. Nowoczesne rozwiązania takie jak automatyka przemysłowa czy Internet Rzeczy (IoT) zaczynają odgrywać coraz większą rolę w optymalizacji procesów związanych z wykorzystaniem tych maszyn. Dzięki zastosowaniu czujników i systemów monitorujących możliwe jest bieżące śledzenie parametrów pracy maszyn oraz natychmiastowe reagowanie na wszelkie nieprawidłowości. Integracja maszyn pneumatycznych z systemami zarządzania produkcją pozwala na lepsze planowanie i koordynację działań w zakładzie przemysłowym. Dodatkowo nowoczesne oprogramowanie umożliwia symulacje pracy maszyn oraz analizy wydajności, co pozwala na identyfikację obszarów wymagających poprawy. Warto również wspomnieć o postępach w zakresie materiałów wykorzystywanych do budowy komponentów maszyn pneumatycznych, które stają się coraz bardziej wytrzymałe i odporne na działanie wysokich ciśnień oraz temperatur.
Jakie są kluczowe różnice między maszynami pneumatycznymi a hydraulicznymi
Maszyny pneumatyczne i hydrauliczne to dwa różne systemy, które są często porównywane ze względu na ich zastosowanie w przemyśle. Kluczową różnicą między nimi jest medium robocze. W przypadku maszyn pneumatycznych wykorzystywane jest sprężone powietrze, podczas gdy maszyny hydrauliczne działają na zasadzie cieczy, najczęściej oleju. Ta różnica ma istotny wpływ na właściwości obu systemów. Maszyny pneumatyczne są zazwyczaj lżejsze i bardziej elastyczne, co sprawia, że są idealne do zastosowań wymagających szybkiego ruchu oraz precyzyjnej regulacji. Z kolei maszyny hydrauliczne oferują znacznie większą moc roboczą, co czyni je bardziej odpowiednimi do zadań wymagających dużych sił, takich jak przenoszenie ciężkich ładunków. Kolejnym aspektem jest koszt eksploatacji. Systemy pneumatyczne są często tańsze w utrzymaniu, ponieważ nie wymagają skomplikowanych układów uszczelniających ani zbiorników na ciecz. Jednakże, sprężone powietrze może być mniej efektywne w niektórych aplikacjach, gdzie wymagana jest stała moc i precyzyjne sterowanie.
Jakie są najnowsze trendy w budowie maszyn pneumatycznych
W ostatnich latach można zaobserwować wiele interesujących trendów w budowie maszyn pneumatycznych, które mają na celu zwiększenie ich efektywności oraz dostosowanie do nowoczesnych wymagań przemysłowych. Jednym z najważniejszych kierunków rozwoju jest automatyzacja procesów produkcyjnych, która pozwala na minimalizację błędów ludzkich oraz zwiększenie wydajności. W tym kontekście coraz częściej stosuje się systemy sterowania oparte na sztucznej inteligencji oraz uczeniu maszynowym, które umożliwiają optymalizację pracy maszyn w czasie rzeczywistym. Dodatkowo rośnie znaczenie zrównoważonego rozwoju i efektywności energetycznej, co prowadzi do poszukiwania nowych rozwiązań technologicznych zmniejszających zużycie energii oraz emisję hałasu. Wiele firm inwestuje w rozwój materiałów kompozytowych i lekkich stopów metali, które pozwalają na budowę bardziej kompaktowych i wydajnych urządzeń. Również integracja z systemami IoT staje się coraz bardziej powszechna, co umożliwia zdalne monitorowanie stanu maszyn oraz przewidywanie awarii przed ich wystąpieniem.
Jakie są wyzwania związane z eksploatacją maszyn pneumatycznych
Eksploatacja maszyn pneumatycznych wiąże się z szeregiem wyzwań, które mogą wpływać na ich efektywność oraz niezawodność. Jednym z głównych problemów jest konieczność zapewnienia odpowiedniego ciśnienia sprężonego powietrza przez cały czas pracy maszyny. Niewłaściwe ciśnienie może prowadzić do spadku wydajności lub nawet uszkodzenia komponentów. Dodatkowo sprężone powietrze musi być odpowiednio filtrowane i osuszane, aby uniknąć zanieczyszczeń oraz kondensatu, które mogą negatywnie wpłynąć na działanie systemu. Kolejnym wyzwaniem jest regularna konserwacja maszyn, która jest niezbędna dla zapewnienia ich długotrwałej pracy. Wymiana uszczelek, smarowanie ruchomych części czy kontrola stanu filtrów to tylko niektóre z czynności, które należy wykonywać regularnie. Ponadto operatorzy muszą być odpowiednio przeszkoleni w zakresie obsługi tych maszyn, aby uniknąć błędów mogących prowadzić do awarii lub wypadków.
Jakie są perspektywy rozwoju technologii pneumatycznych w przyszłości
Perspektywy rozwoju technologii pneumatycznych w przyszłości wyglądają obiecująco dzięki ciągłym innowacjom oraz rosnącemu zapotrzebowaniu na automatyzację procesów przemysłowych. W miarę jak przemysł 4.0 staje się coraz bardziej popularny, technologia pneumatyczna będzie musiała dostosować się do nowych wymagań związanych z integracją z systemami cyfrowymi i inteligentnymi rozwiązaniami. Możliwość monitorowania pracy maszyn w czasie rzeczywistym oraz analizy danych pozwoli na optymalizację procesów produkcyjnych i zwiększenie efektywności energetycznej. Dodatkowo rozwój materiałów kompozytowych i nanotechnologii może przyczynić się do stworzenia lżejszych i bardziej wytrzymałych komponentów maszyn pneumatycznych, co wpłynie na ich wydajność i niezawodność. Warto również zauważyć rosnącą rolę ekologicznych rozwiązań w przemyśle, co skłoni producentów do poszukiwania bardziej zrównoważonych metod produkcji sprężonego powietrza oraz redukcji hałasu generowanego przez maszyny pneumatyczne.
Jakie są kluczowe czynniki wpływające na wybór maszyn pneumatycznych
Wybór odpowiednich maszyn pneumatycznych do konkretnego zastosowania zależy od wielu czynników, które należy dokładnie przeanalizować przed podjęciem decyzji. Przede wszystkim istotne jest określenie wymagań dotyczących mocy roboczej oraz wydajności maszyny w kontekście planowanego zastosowania. Należy również uwzględnić dostępność sprężonego powietrza oraz jego jakość, ponieważ niewłaściwe ciśnienie lub zanieczyszczenia mogą negatywnie wpłynąć na działanie systemu. Koszt zakupu oraz eksploatacji maszyny to kolejny ważny aspekt – warto porównać różne modele pod kątem ceny zakupu oraz kosztów związanych z serwisowaniem i konserwacją. Również elastyczność maszyny w kontekście ewentualnych zmian produkcji czy dostosowywania do nowych warunków pracy ma znaczenie dla długoterminowej opłacalności inwestycji. Nie można zapominać o aspektach ergonomicznych – maszyny powinny być łatwe w obsłudze i dostosowane do potrzeb operatora, aby zwiększyć komfort pracy i bezpieczeństwo użytkowników.